The Secret Ingredient to Winning Formulations Formulators in the paints, coatings, and adhesives markets face…
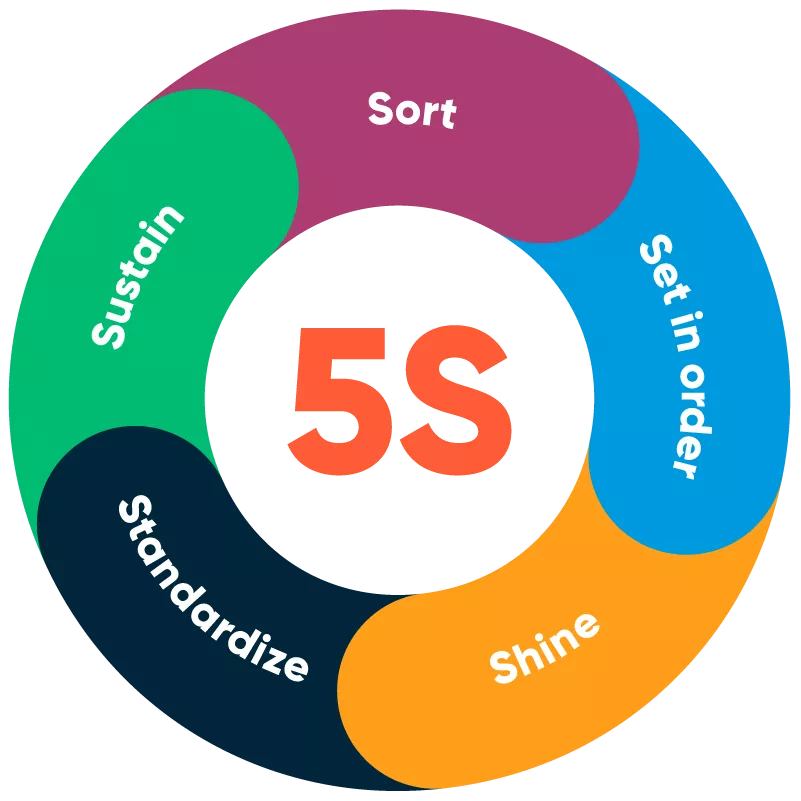
5s methodology – what is it?
Here at STI Polymer we practice 5S, a five-step methodology that helps create a more organized and productive workspace. The 5 pillars of this methodology are, Sort (Seiri), Set in Order (Seiton), Shine (Seiso), Standardize (Seiketsu), and Sustain (Shitsuke).
1. Seiri (Sort): This involves sorting through all items in a workspace and removing unnecessary items, keeping only what is essential for the current operation.
2. Seiton (Set in Order): Once unnecessary items are removed, the next step is to organize the remaining items in a structured and efficient manner. This includes labeling items, arranging them logically, and ensuring they are easily accessible.
3. Seiso (Shine): This step focuses on cleanliness and involves thoroughly cleaning the workspace and equipment. Regular cleaning helps prevent equipment malfunction and ensures a safe working environment.
4. Seiketsu (Standardize): Standardization involves establishing clear and consistent procedures for maintaining the first three steps (Sort, Set in Order, Shine). This ensures that the workplace remains organized and clean over time.
5. Shitsuke (Sustain): Sustainment is about maintaining the improvements achieved through the first four steps. It involves creating a culture of continuous improvement, where employees are encouraged to adhere to the 5S principles and regularly identify opportunities for further improvement.
Following the 5S methodology helps improve our efficiency, increase safety and allows for continuous improvement.